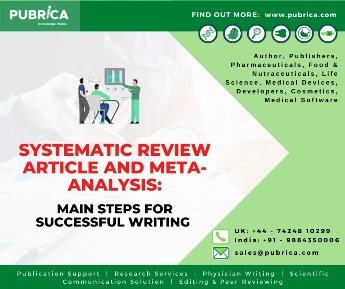
Systematic review article andMeta-analysis: Main steps for Successful writing
August 9, 2021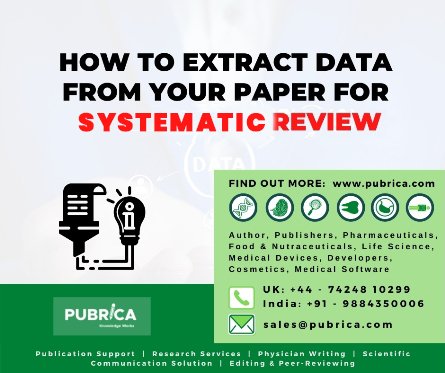
How to extract data from your paper for systematic review
August 16, 2021In brief
With increasing number of patients and diseases, the need for medicines is growing more than ever. This has created pressure on the pharmaceutical industries to product high quality of medicines. Tablets are a form of medicine which is solid and is given as oral dosage. Tablets are the highest selling dosage form of medicine. Tablets are produced by mixing excipients and active pharmaceutical ingredient (API). The powder mixture is then compressed and a tablet in a solid form is obtained. A good tablet is free from any sort of defects (pharmaguideline, 2017). Common issues faced in the product development processes of tablets are as weight variation, hardness, friability, picking, laminating, mottling, sticking, capping, chipping, and double press or impression (Jonathan Gaik, 2018). Among these mentioned defects laminating/capping, hardness, and picking/sticking are the three most commonly encountered issues faced in the production process of making tablets. Generally, these defects stem from various issues in production process with unit upstream, tablet press, compression failure, and prevention of proper ejection of the product if it is too wet or too dry. Other issues include Poor quality of raw materials, formation of too many fines in the milling process, defects in formulation process. bad compressibility and flow of the powder (Rajani et al., 2018).
- Capping
Capping phenomena occurs when there is fracture at the top of the tablet. The top layer gets separated and detached from the solid tablet body. This issue generally arises when air is trapped in the tablets powder material during the compression stage. Capping can also stem from the issue of failure of compression of the formulation because of accumulation of powder fines (Jonathan Gaik, 2018).
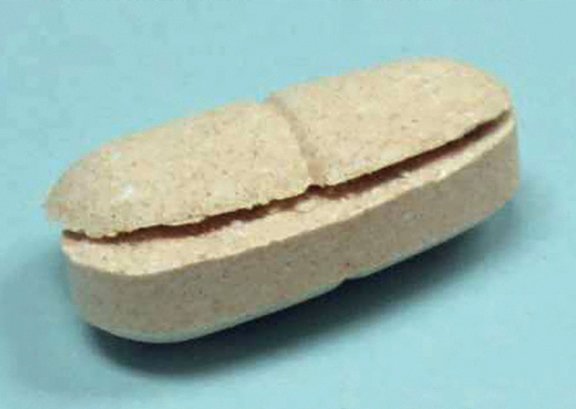
Figure 1 : Capping defect (Rana & Kumar, 2013)
- Lamination
The term lamination is used when a split occurs anywhere in the tablet other than the top layer. Usually, lamination defect is similar to capping and caused by the same issues. Nevertheless, it is essential to diagnose the issue of lamination in a proper manner. Often, lamination occurs due to over compression of the tablets. As greater compression can cause the granules to flatten out and thus prevent them from binding together. Lamination may also occur when fine or light particles do not combine, as the particles fail to compress well (Jonathan Gaik, 2018).
- Sticking and Picking
The defect of sticking happens when the formulation granules stick to the face of the press punch. Quite differently, picking defect occurs when the mixture granules stick on the design embossing of the punch tip such as in logos or lettering. Both picking and sticking result in the production of defective tablets. In quality control of the tablets, generally a visual inspection is carried out to identify picking and sticking. However, this method of visual inspection is very time-consuming and tends to decrease the overall production yield of the tablet. Unfortunately sometimes many manufacturers have no option but to carry out visual detection as a quality control measure. When, the batch of the product reach the compression stage, the skilled operator should efficiently adjust the press to comply with the product’s characteristic designs. The quality of the product is majorly affected by the tablet’s press setup, operation, tooling, and maintenance. There may be cases when the granules are not completely dried, in other words they may be hard and dry on the outside but wet and moist inside. This scenario in turn seriously affects the tablet’s quality. The un dried particles can break open during compression and stick to the punch press surfaces causing sticking.. In such cases it is essential to keep checking the process of drying the granules (Rajani et al., 2018; Chattoraj et al., 2018).
- Tablet Hardness
Another issue arising in tablet production process is the variation in the hardness of the tablets. A soft tablet tends to cause a range of issues not only in the press process but also in the consistency of the product. A soft tablet can lead to product recall due to poor film coating process and packaging of the product (Rajani et al., 2018).
Conclusion:
Tablet manufacture is shown significantly increase the likelihood of tablet defects through breakage of tablets. Increasing tablet tensile strength provides some resistance to defects upon impact. The remedies are change the solvent system, change the binder, reduce drying temperature and use a smaller particle size, improperly mixed dye especially during direct compression. Mix it properly and reduce size if it is of a larger size to prevent segregation. Tablets are widely used dosage forms but defects in aesthetic appearance may lead to rejection of their administration by patient. Be careful during manufacturing process. The cost vs benefit equation mainly focuses on the pharmaceutical innovations which will be an integral part to address this challenge. The adequacies of drug benefit programs and policies that foster investment in newer medicines pay way for the new pharmaceutical environment.
References
Chattoraj, S., Daugherity, P., McDermott, T., Olsofsky, A., Roth, W.J. & Tobyn, M. (2018). Sticking and Picking in Pharmaceutical Tablet Compression: An IQ Consortium Review. Journal of Pharmaceutical Sciences. [Online]. 107 (9). pp. 2267–2282. Available from: https://linkinghub.elsevier.com/retrieve/pii/S0022354918302922.
Jonathan Gaik (2018). Tablets and capsules Soild doed Digest. [Online]. Available from: https://www.tabletscapsules.com/enews_tc/2018/issues/tcnews_11_26_18question.html.
pharmaguideline (2017). Different Types of Defects of Tablets. [Online]. 2017. Available from: https://www.pharmaguideline.com/2017/09/different-types-of-defects-of-tablets.html.
Rajani, C., Kumar, D.D., Jaya, D. & Kumar, J.A. (2018). Effects of granule particle size and lubricant concentration on tablet hardness containing large concentration of polymers. Brazilian Journal of Pharmaceutical Sciences. [Online]. 53 (3). Available from: http://www.scielo.br/scielo.php?script=sci_arttext&pid=S1984-82502017000300617&lng=en&tlng=en.
Rana, A.S. & Kumar, S.L.H. (2013). Manufacturing defects of tablets-a review. Journal of Drug Delivery and Therapeutics. [Online]. 3 (6). pp. 200–206. Available from: http://jddtonline.info/index.php/jddt/article/view/722.